Are you tired of your favorite knife rusting away after exposure to moisture? Do you need a reliable blade that can withstand wet conditions? Look no further! In this comprehensive guide, we’ll dive deep into the world of corrosion-resistant knife steels, exploring the best materials for use in damp environments. Whether you’re a seasoned outdoorsman, a professional chef, or simply someone who wants a durable everyday carry knife, this article will equip you with the knowledge to choose the perfect blade for your needs.
Why This Guide Matters
Understanding knife steel corrosion resistance is crucial for anyone who uses knives in humid or wet conditions. The right choice of steel can mean the difference between a blade that lasts for years and one that quickly succumbs to rust and pitting. We’ll explore the science behind corrosion resistance, compare different steel types, and provide practical advice for maintaining your knife in challenging environments.
The Science of Corrosion in Knife Steels
Corrosion is the enemy of every knife enthusiast. But what exactly causes it? At its core, corrosion is an electrochemical process where iron in the steel reacts with oxygen and water to form iron oxide, commonly known as rust. This process is accelerated in the presence of salt, acids, and other corrosive substances.In knife steels, the composition plays a crucial role in determining corrosion resistance. The primary alloying element that enhances corrosion resistance is chromium. When present in sufficient quantities (typically 13% or more), chromium forms a thin, invisible layer of chromium oxide on the surface of the steel. This passive layer acts as a barrier, protecting the underlying metal from further oxidation.
What Makes a Steel Corrosion-Resistant?
Several factors contribute to a steel’s corrosion resistance:
- Chromium Content: As mentioned, chromium is the star player in corrosion resistance. The higher the chromium content, the more resistant the steel is to rust.
- Other Alloying Elements: Elements like molybdenum, nitrogen, and vanadium can enhance corrosion resistance when added in the right proportions.
- Carbon Content: While carbon improves hardness and edge retention, it can reduce corrosion resistance if present in high amounts.
- Microstructure: The way the steel is processed and heat-treated affects its microstructure, which in turn influences corrosion resistance.
- Surface Finish: A smooth, polished surface is less likely to trap moisture and corrosive agents, thus improving resistance.
Understanding these factors can help you make an informed decision when choosing a knife for wet environments.
Stainless vs. Carbon Steel: Which is Better for Wet Environments?
When it comes to corrosion resistance, stainless steel is generally superior to carbon steel. Stainless steels contain a minimum of 13% chromium, which forms that protective oxide layer we discussed earlier. This makes them much more resistant to rust and corrosion, especially in wet conditions.However, it’s not a clear-cut victory for stainless steel across the board. Here’s a comparison:Stainless Steel Pros:
- Excellent corrosion resistance
- Low maintenance
- Good for saltwater environments
Stainless Steel Cons:
- Generally softer than carbon steel
- May not hold an edge as well
- Can be more difficult to sharpen
Carbon Steel Pros:
- Typically harder
- Holds a sharper edge for longer
- Easier to sharpen
Carbon Steel Cons:
- Highly susceptible to rust and corrosion
- Requires regular maintenance
- Not ideal for wet or marine environments
For most users in wet environments, a high-quality stainless steel will be the better choice. However, with proper care and maintenance, some carbon steels can still perform well in damp conditions.
Top 5 Corrosion-Resistant Knife Steels
Now, let’s dive into some specific steel types that excel in corrosion resistance:
- H1 Steel: This nitrogen-based steel is virtually immune to rust, making it ideal for marine environments. It’s often used in dive knives and fishing knives.
- LC200N: Another nitrogen steel, LC200N offers excellent corrosion resistance along with good edge retention and toughness.
- 440C: A classic high-carbon stainless steel, 440C provides a good balance of corrosion resistance and edge retention.
- VG-10: This Japanese stainless steel is known for its excellent corrosion resistance and ability to take a sharp edge.
- S35VN: A premium stainless steel that offers outstanding corrosion resistance along with excellent edge retention and toughness.
Each of these steels has its own unique properties, so consider your specific needs when making a choice.
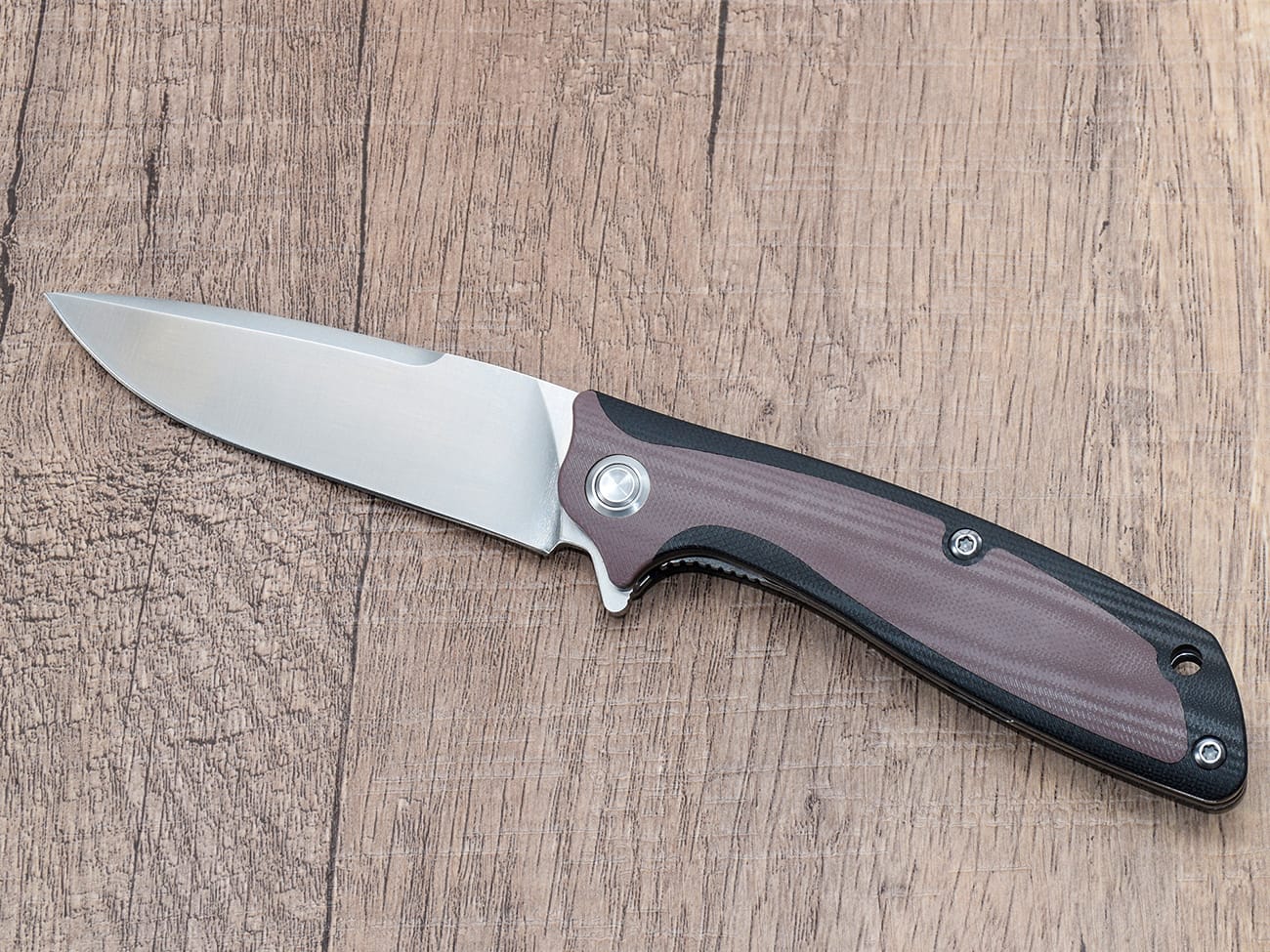
A custom 9cr18mov stainless steel pocket knife with G10 handle, offering good corrosion resistance for everyday use
How Does Heat Treatment Affect Corrosion Resistance?
Heat treatment is a critical process in knife making that can significantly impact a blade’s properties, including its corrosion resistance. The heat treatment process involves heating the steel to a specific temperature and then cooling it in a controlled manner. This alters the steel’s microstructure, affecting its hardness, toughness, and corrosion resistance.For corrosion-resistant steels, proper heat treatment is essential to achieve the optimal balance between hardness and corrosion resistance. Improper heat treatment can lead to a blade that’s either too soft (compromising edge retention) or too brittle (risking chipping or breaking). It can also negatively impact the formation of the protective chromium oxide layer in stainless steels.When choosing a knife, especially a high-end one, it’s worth considering the reputation of the manufacturer for their heat treatment processes. A well-heat-treated blade from a less corrosion-resistant steel may outperform a poorly heat-treated blade from a more corrosion-resistant steel.
Are There Any Downsides to Highly Corrosion-Resistant Steels?
While corrosion resistance is a valuable trait, it’s important to understand that there can be trade-offs. Here are some potential downsides to consider:
- Edge Retention: Some highly corrosion-resistant steels may not hold an edge as well as their less resistant counterparts. This is because the alloying elements that enhance corrosion resistance can sometimes reduce the steel’s ability to maintain a sharp edge.
- Hardness: Corrosion-resistant steels are often softer than high-carbon steels, which can affect their performance in heavy-duty cutting tasks.
- Sharpening Difficulty: Many stainless steels are more challenging to sharpen than carbon steels due to their composition and hardness.
- Cost: High-performance corrosion-resistant steels are often more expensive than simpler carbon steels.
- Wear Resistance: Some corrosion-resistant steels may have lower wear resistance, meaning they might not stand up as well to abrasive materials.
It’s important to weigh these factors against your specific needs. For many users, the benefits of corrosion resistance outweigh these potential drawbacks, especially in wet environments.
Caring for Your Knife in Wet Environments
Even with a corrosion-resistant steel, proper care is essential to maintain your knife’s performance and longevity. Here are some tips for caring for your knife in wet conditions:
- Dry Your Knife: After use in wet conditions, always dry your knife thoroughly. Pay special attention to the pivot area in folding knives.
- Oil Regularly: Apply a thin coat of food-safe mineral oil or specialized knife oil to the blade and other metal parts.
- Clean After Saltwater Exposure: If your knife has been exposed to saltwater, rinse it with fresh water and dry it immediately.
- Store Properly: Keep your knife in a dry place when not in use. Consider using silica gel packets in your storage area to absorb moisture.
- Regular Maintenance: Periodically disassemble your knife (if it’s a folder) to clean and lubricate all parts.
- Avoid Prolonged Moisture Exposure: Even with corrosion-resistant steel, try to minimize extended exposure to moisture when possible.
By following these care tips, you can significantly extend the life of your knife, regardless of the steel type.
Budget-Friendly Options for Corrosion-Resistant Knives
Not everyone can afford premium steels like S35VN or LC200N. Fortunately, there are several budget-friendly options that offer good corrosion resistance:
- 8Cr13MoV: A Chinese stainless steel that offers decent corrosion resistance and is easy to sharpen.
- AUS-8: A Japanese steel known for its good balance of corrosion resistance, edge retention, and ease of sharpening.
- 420HC: An improved version of 420 stainless steel, offering better corrosion resistance and edge retention.
- 14C28N: A Scandinavian stainless steel that provides excellent corrosion resistance at a reasonable price point.
- 9Cr18MoV: Another Chinese stainless steel that offers good corrosion resistance and edge retention.
These steels may not match the performance of premium options, but they provide good corrosion resistance at a more accessible price point. They’re excellent choices for beginners or those on a tight budget who still need a reliable knife for wet environments.
Specialized Steels for Extreme Conditions
For those facing the most challenging environments, there are specialized steels designed to withstand extreme conditions:
- H1 and LC200N: As mentioned earlier, these nitrogen-based steels are virtually rustproof, making them ideal for marine environments, dive knives, and rescue tools.
- Vanax SuperClean: A powder metallurgy stainless steel with exceptional corrosion resistance and edge retention, suitable for harsh marine environments.
- NIOLOX: A German stainless steel that offers excellent corrosion resistance along with good wear resistance and toughness.
- ZDP-189: While primarily known for its extreme edge retention, this steel also offers very good corrosion resistance.
- RWL34: A powder metallurgy stainless steel that provides excellent corrosion resistance and edge holding ability.
These specialized steels often come with a higher price tag, but for those working in extreme conditions or demanding the absolute best performance, they can be worth the investment.
Making the Right Choice: Factors to Consider
Choosing the right corrosion-resistant steel for your knife involves considering several factors:
- Intended Use: Will you be using the knife for everyday carry, in the kitchen, for outdoor adventures, or in a marine environment?
- Maintenance Willingness: How much time and effort are you willing to put into maintaining your knife?
- Budget: High-end corrosion-resistant steels can be expensive. Determine how much you’re willing to spend.
- Edge Retention Needs: Consider how often you’re willing to sharpen your knife versus how long you need it to hold an edge.
- Local Climate: If you live in a particularly humid or coastal area, corrosion resistance might be a top priority.
- Personal Preference: Some users prefer the patina that develops on carbon steels, while others prefer the consistently clean look of stainless steels.
By carefully considering these factors, you can choose a knife steel that best meets your needs for corrosion resistance and overall performance.
Conclusion
Choosing the right corrosion-resistant knife steel for wet environments doesn’t have to be a daunting task. By understanding the science behind corrosion resistance, the properties of different steel types, and considering your specific needs, you can make an informed decision that will serve you well for years to come.Remember, even the most corrosion-resistant steel benefits from proper care and maintenance. With the right combination of steel choice and knife care, you’ll have a reliable tool ready to tackle any wet environment you encounter.
Key Takeaways:
- Chromium content is crucial for corrosion resistance in knife steels.
- Stainless steels generally outperform carbon steels in wet environments.
- Top corrosion-resistant steels include H1, LC200N, 440C, VG-10, and S35VN.
- Proper heat treatment is essential for optimal corrosion resistance.
- Regular maintenance is key to prolonging your knife’s life, regardless of steel type.
- Budget-friendly options like 8Cr13MoV and AUS-8 offer good corrosion resistance.
- Consider factors like intended use, maintenance willingness, and budget when choosing a knife steel.
Armed with this knowledge, you’re now ready to choose the perfect corrosion-resistant knife for your needs. Happy knife hunting!