Knives are more than just tools; they are a blend of craftsmanship, precision, and functionality. Whether you’re a chef, an outdoor enthusiast, or a collector, understanding how knives are made can deepen your appreciation for these essential tools. This article takes you inside a professional knife factory, exploring the intricate processes, materials, and expertise that go into crafting high-quality knives. From blade sharpening to custom engraving, you’ll discover what makes a knife truly exceptional and why choosing the right factory matters.
Table of Contents
1. What Makes a Knife Factory Professional?
A professional knife factory is defined by its commitment to quality, innovation, and precision. These factories specialize in producing knives that meet the highest standards for performance and durability. Here are some key features of a professional knife factory:
- Advanced Manufacturing Techniques: From traditional forging to modern CNC machining, professional factories use cutting-edge methods to ensure consistency and precision.
- Skilled Craftsmen: Experienced artisans oversee critical steps like blade sharpening, heat treatment, and handle assembly.
- Premium Materials: High-quality steel, such as carbon steel or stainless steel, is used to create blades with superior edge retention and corrosion resistance.
Choosing a factory with these qualities ensures that your knife will perform reliably, whether it’s a chef’s knife or a tactical tool.
2. How Are Knives Made in a Factory?
The process of making knives in a factory involves several meticulous steps. Here’s an overview of the key stages:
Blade Forging and Shaping
The blade starts as a raw piece of steel. Depending on the knife type, the steel may be forged, stamped, or laser-cut into shape. Forging involves heating the steel to high temperatures and hammering it into the desired form, a method that enhances the blade’s strength and durability.
Heat Treatment
Heat treatment is a critical step that determines the blade’s hardness and flexibility. The steel is heated to a specific temperature and then rapidly cooled, a process known as quenching. This step ensures the blade can hold a sharp edge without becoming brittle.
Blade Sharpening
After heat treatment, the blade is ground and sharpened to achieve a razor-sharp edge. Factories often use precision machines for this step, but final touches may be done by hand to ensure perfection.
Handle Assembly
The handle is attached to the blade using materials like wood, G10, or micarta. The choice of handle material affects the knife’s grip, balance, and overall aesthetic.
3. What Materials Are Used in Knife Manufacturing?
The materials used in knife manufacturing play a significant role in the knife’s performance and durability. Here are some common materials:
Blade Materials
- Stainless Steel: Resistant to rust and corrosion, ideal for kitchen knives.
- Carbon Steel: Known for its sharpness and edge retention, often used in chef’s knives.
- Damascus Steel: A premium material with a distinctive wavy pattern, combining beauty and functionality.
Handle Materials
- Wood: Offers a classic look and comfortable grip.
- G10: A lightweight, durable composite material.
- Micarta: A resin-based material known for its strength and texture.
4. Why Is Blade Sharpening Important?
A knife’s performance depends heavily on its sharpness. Blade sharpening ensures that the knife can cut through materials with minimal effort. Factories use specialized equipment to achieve precise angles and edges. Regular sharpening is also essential for maintaining the knife’s performance over time.
5. What Are the Benefits of Custom Knives?
Custom knives offer a level of personalization and uniqueness that mass-produced knives cannot match. Here are some benefits of choosing custom knives:
- Tailored Design: You can select the blade shape, handle material, and other features to suit your specific needs.
- Engraving Options: Add a personal touch with custom engravings, such as your name or logo.
- Enhanced Performance: Custom knives are often made with premium materials and craftsmanship, ensuring superior performance.
For example, a custom folding knife with a G10 handle and liner lock can be designed for both functionality and style.
6. How to Choose the Right Knife Factory?
Selecting the right knife factory is crucial for ensuring quality and reliability. Here are some factors to consider:
- Reputation: Look for factories with a proven track record of producing high-quality knives.
- Specialization: Some factories specialize in specific types of knives, such as kitchen knives or tactical tools.
- Customization Options: Choose a factory that offers custom knife designs and engraving services.
For example, HT Pocket Knife is a trusted name in the industry, offering a wide range of custom knives and EDC tools.
7. What Are the Popular Types of Knives?
Knife factories produce a variety of knives to meet different needs. Here are some popular types:
- Chef’s Knives: Designed for precision cutting in the kitchen.
- Folding Knives: Compact and versatile, ideal for everyday carry.
- Fixed Blade Knives: Durable and robust, perfect for outdoor activities.
Each type of knife is crafted with specific features and materials to enhance its performance.
8. How Are Knives Tested for Quality?
Quality control is a critical aspect of knife manufacturing. Factories use rigorous testing methods to ensure each knife meets the required standards. These tests may include:
- Edge Retention Tests: Measuring how long the blade stays sharp during use.
- Corrosion Resistance Tests: Ensuring the blade can withstand exposure to moisture and chemicals.
- Handle Durability Tests: Checking the handle’s strength and grip under various conditions.
9. What Are the Latest Trends in Knife Manufacturing?
The knife industry is constantly evolving, with new trends and innovations emerging. Here are some of the latest trends:
- Sustainable Materials: Factories are increasingly using eco-friendly materials for handles and packaging.
- Advanced Coatings: Blades are now coated with materials like titanium for enhanced durability and aesthetics.
- Smart Knives: Some factories are experimenting with knives that incorporate smart technology, such as sensors for tracking usage.
10. Why Trust Professional Knife Factories?
Trusting a professional knife factory ensures that you receive a product that meets your expectations. These factories prioritize:
- Quality Assurance: Every knife undergoes strict quality control checks.
- Customer Satisfaction: Professional factories value their customers and strive to meet their needs.
- Innovation: Leading factories invest in research and development to create better products.
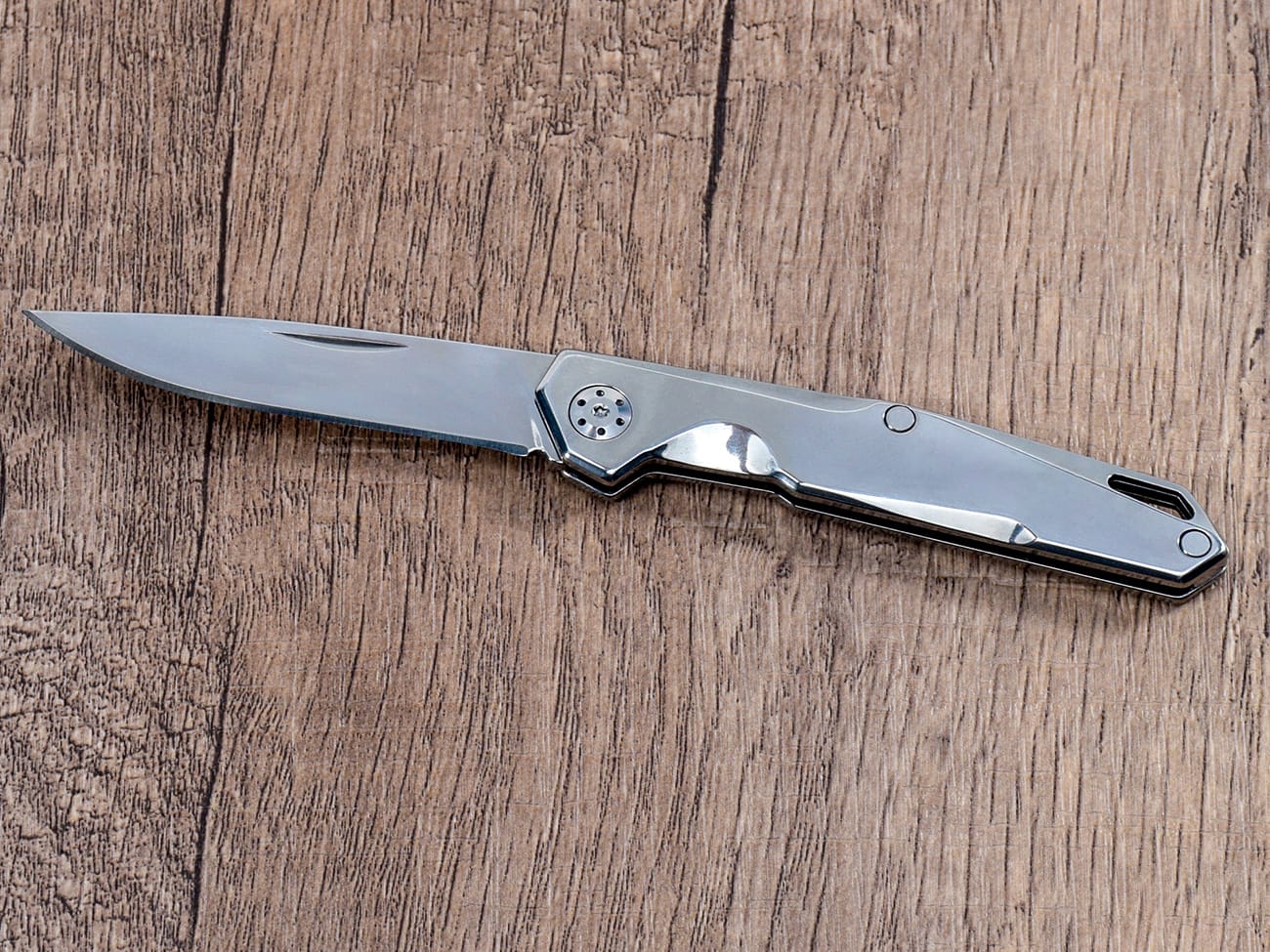
Alt: Custom Folding Knife with Stainless Steel Handle and Liner Lock
Key Takeaways
- A professional knife factory combines craftsmanship, precision, and innovation to produce high-quality knives.
- The knife manufacturing process includes steps like blade forging, heat treatment, and handle assembly.
- Materials like stainless steel, carbon steel, and G10 are commonly used for blades and handles.
- Custom knives offer personalization and superior performance.
- Trusting a reputable factory ensures quality, reliability, and customer satisfaction.
For more information, check out these resources: