Are you curious about the cutting-edge technology that’s reshaping the knife industry? Look no further than CNC knives. These marvels of engineering combine traditional craftsmanship with computer-controlled precision, offering unparalleled accuracy and versatility. In this comprehensive guide, we’ll explore the world of CNC knives, their applications, and why they’re becoming an essential tool for professionals and enthusiasts alike. Whether you’re a seasoned knife collector or simply interested in the latest advancements in cutting technology, this article will provide valuable insights into the fascinating realm of CNC knives.
What Exactly is a CNC Knife?
CNC, which stands for Computer Numerical Control, refers to the automated control of machining tools using computer programming. When applied to knife making, this technology allows for incredibly precise and consistent cuts. A CNC knife is essentially a cutting tool that operates under computer guidance, enabling it to perform complex cutting tasks with remarkable accuracy.
The Evolution of Knife Making: From Hand-Forged to CNC Precision
Traditional knife making has been a skilled craft for centuries, but how has CNC technology changed the game? Let’s explore the journey from artisanal blade crafting to modern CNC knife production.
How Does a CNC Knife Work?
Understanding the mechanics behind CNC knives is crucial to appreciating their capabilities. We’ll break down the process step-by-step, from digital design to the final cut.
What Are the Different Types of CNC Knives?
CNC technology has given rise to various specialized cutting tools. We’ll examine the most common types, including drag knives, oscillating knives, and tangential knives, discussing their unique features and applications.
What Materials Can CNC Knives Cut?
One of the most impressive aspects of CNC knives is their versatility. From paper and fabric to carbon fiber and metals, we’ll explore the wide range of materials that can be precisely cut using CNC technology.
What Industries Benefit from CNC Knife Cutting?
CNC knives have found applications across numerous sectors. We’ll delve into how industries such as automotive, aerospace, textile, and even artisanal knife making are leveraging this technology to improve their products and processes.
What Are the Advantages of Using a CNC Knife?
Precision, consistency, and efficiency are just a few of the benefits offered by CNC knives. We’ll examine these advantages in detail and discuss how they’re transforming various industries.
Are There Any Limitations to CNC Knife Technology?
While CNC knives offer numerous benefits, it’s important to understand their limitations. We’ll provide a balanced view by discussing potential drawbacks and scenarios where traditional cutting methods might still be preferred.
How to Choose the Right CNC Knife for Your Needs?
With various CNC knife options available, selecting the right one for your specific requirements can be challenging. We’ll offer guidance on factors to consider when choosing a CNC knife, including cutting depth, material compatibility, and software integration.
What Does the Future Hold for CNC Knife Technology?
As technology continues to advance, what can we expect from the next generation of CNC knives? We’ll explore emerging trends and potential innovations that could further revolutionize the cutting industry.
Unable to render image
The Precision of CNC Knives: A Game-Changer in Cutting Technology
CNC knives have revolutionized the cutting industry by offering unparalleled precision and consistency. Unlike traditional cutting methods, which rely heavily on the skill and steadiness of the operator’s hand, CNC knives utilize computer-controlled movements to execute cuts with microscopic accuracy. This level of precision is particularly crucial in industries where even the slightest deviation can result in significant losses or compromised product quality.For instance, in the automotive industry, CNC knives play a crucial role in cutting intricate designs and patterns for vehicle interiors. The ability to reproduce complex shapes with exact dimensions ensures that each piece fits perfectly, contributing to the overall quality and aesthetics of the final product. Similarly, in the aerospace sector, where tolerances are measured in fractions of a millimeter, CNC knives are indispensable for cutting composite materials used in aircraft construction.The precision offered by CNC knives also extends to the world of custom knife making. Artisanal knife makers can now use CNC technology to create intricate blade designs or handle patterns that would be extremely challenging to produce consistently by hand. This marriage of traditional craftsmanship and modern technology allows for the creation of unique, high-quality knives that combine artistic expression with functional precision.
Versatility: The Hallmark of CNC Knife Cutting
One of the most significant advantages of CNC knives is their versatility in terms of the materials they can cut. From soft fabrics and paper to tough materials like carbon fiber and even certain metals, CNC knives can handle a wide range of cutting tasks. This versatility makes them an invaluable tool across various industries and applications.In the textile industry, for example, CNC knives have transformed the process of pattern cutting. Complex clothing designs that once required hours of meticulous hand-cutting can now be executed quickly and accurately using CNC technology. This not only speeds up production but also reduces material waste, as the precision cutting minimizes errors and offcuts.The versatility of CNC knives also shines in the packaging industry. These machines can cut and score cardboard, foam, and plastic materials to create custom packaging solutions. The ability to switch between different cutting tools and adjust cutting parameters allows for the production of packaging that is both functional and visually appealing.Even in the realm of artistic expression, CNC knives have found their place. Artists and designers use these tools to create intricate paper cuts, stencils, and mixed-media artworks. The precision and repeatability of CNC cutting enable artists to produce limited edition pieces with consistent quality.
Efficiency and Productivity: The CNC Advantage
In today’s fast-paced manufacturing environment, efficiency is key, and CNC knives deliver on this front. Once programmed, a CNC knife can operate continuously, producing identical cuts with minimal human intervention. This level of automation not only increases productivity but also reduces the likelihood of human error, ensuring consistent quality across large production runs.For businesses dealing with custom orders or short production runs, CNC knives offer the flexibility to quickly switch between different cutting patterns without the need for extensive retooling. This adaptability is particularly valuable in industries with rapidly changing consumer demands or seasonal product variations.Moreover, the efficiency of CNC knives extends beyond the cutting process itself. Many CNC systems can be integrated with design software, allowing for seamless transition from digital designs to physical products. This integration streamlines the entire production workflow, from concept to final cut, reducing time-to-market for new products.
The Role of CNC Knives in Material Innovation
As new materials are developed for various applications, the need for cutting tools that can handle these materials effectively becomes crucial. CNC knives, with their ability to be precisely controlled and adapted, are at the forefront of working with innovative materials.For instance, in the field of advanced composites, CNC knives are used to cut materials like carbon fiber-reinforced polymers (CFRP) used in aerospace and high-performance automotive applications. The precise control over cutting speed, depth, and angle allows for clean cuts without delamination or fraying of the composite layers.In the realm of pocket knife manufacturing, CNC technology has enabled the use of exotic materials for blade and handle construction. Materials like titanium, G10, and various types of high-performance steels can be cut and shaped with high precision, allowing for the creation of knives with superior performance characteristics.
Challenges and Considerations in CNC Knife Implementation
While the benefits of CNC knives are numerous, implementing this technology does come with its own set of challenges. The initial investment in CNC equipment can be significant, and there’s a learning curve associated with programming and operating these machines effectively.Additionally, while CNC knives excel in precision cutting, they may not always be the most cost-effective solution for simple, high-volume cutting tasks. In such cases, traditional die-cutting methods might still be more economical.Maintenance is another factor to consider. CNC machines require regular upkeep to ensure consistent performance, and downtime for maintenance or repairs can impact production schedules. However, many manufacturers find that the long-term benefits in terms of precision, efficiency, and reduced material waste outweigh these considerations.
The Future of CNC Knife Technology
As we look to the future, the potential for CNC knife technology continues to expand. Advancements in artificial intelligence and machine learning are likely to enhance the capabilities of CNC systems, allowing for even greater precision and adaptability.We may see the development of more specialized CNC knives designed for specific materials or applications. For instance, CNC knives optimized for cutting advanced bio-based materials or next-generation composites could play a crucial role in sustainable manufacturing practices.Integration with other technologies, such as 3D printing and augmented reality, could further revolutionize the design and production process. Imagine a workflow where a product is designed in virtual reality, refined using AI-powered optimization algorithms, and then seamlessly cut using an advanced CNC knife system.
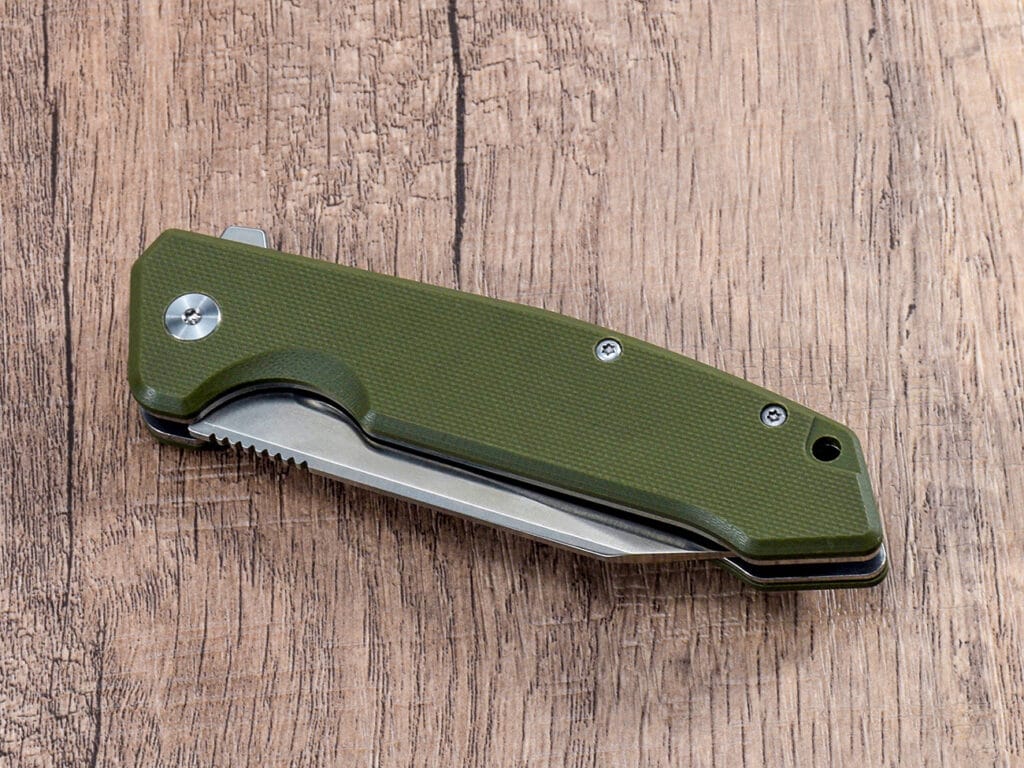
Conclusion: The Cutting Edge of Innovation
CNC knives represent a significant leap forward in cutting technology, offering unparalleled precision, versatility, and efficiency. From the factory floor to the artist’s studio, these tools are reshaping how we approach cutting tasks across a wide range of industries.As we’ve explored in this article, the impact of CNC knives extends far beyond simple cutting. They’re enabling new design possibilities, facilitating work with advanced materials, and driving innovation in manufacturing processes. Whether you’re involved in industrial production, custom knife making, or exploring new creative avenues, understanding the capabilities and potential of CNC knives is crucial in staying at the forefront of your field.As technology continues to evolve, CNC knives will undoubtedly play an increasingly important role in shaping the future of cutting and manufacturing. By embracing these advancements and understanding their applications, we can unlock new possibilities and push the boundaries of what’s possible in precision cutting.
Key Takeaways:
- CNC knives offer unparalleled precision and consistency in cutting.
- They are versatile tools capable of cutting a wide range of materials.
- CNC technology has transformed industries from automotive to artisanal knife making.
- The efficiency and productivity gains from CNC knives can significantly impact manufacturing processes.
- While there are challenges in implementation, the long-term benefits often outweigh the initial investment.
- The future of CNC knife technology promises even greater integration with AI and other advanced technologies.
- Understanding and leveraging CNC knife capabilities is crucial for staying competitive in many industries.